Đúc kim loại là một trong những phương pháp chế tạo cơ khí lâu đời và phổ biến nhất trong công nghiệp. Quá trình này cho phép tạo ra các chi tiết máy và sản phẩm kim loại có hình dạng phức tạp mà khó có thể thực hiện bằng các phương pháp gia công cắt gọt thông thường.
Ngày nay, có nhiều phương pháp đúc kim loại khác nhau được áp dụng rộng rãi, mỗi phương pháp đều có những ưu điểm và hạn chế riêng. Bài viết này sẽ giới thiệu 7 phương pháp đúc kim loại phổ biến nhất hiện nay cùng những đặc điểm nổi bật của từng phương pháp.
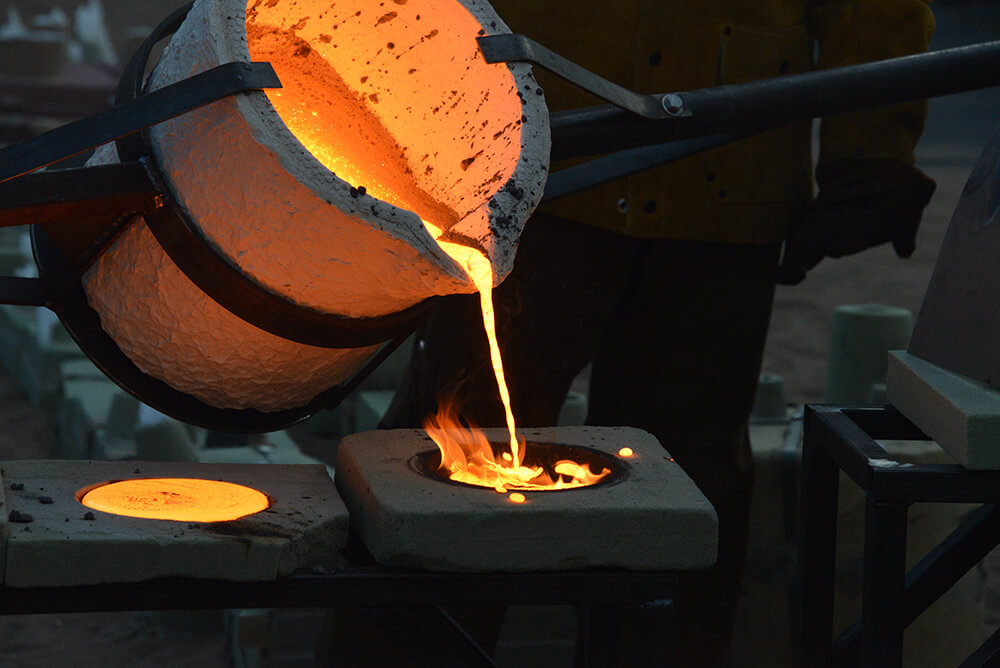
I. Đúc mẫu chảy (Lost wax casting hoặc Investment casting) phương pháp đúc kim loại phổ biến nhất
Còn được gọi là đúc khuôn vỏ mỏng, phương pháp này sử dụng một mẫu sáp hoặc nhựa có hình dạng của sản phẩm cuối cùng. Mẫu này được bao phủ bởi một vật liệu chịu nhiệt, sau đó được nung chảy và thay thế bằng kim loại nóng chảy. Phương pháp này cho phép tạo ra các chi tiết có hình dạng phức tạp và độ chính xác cao.
Đặc điểm nổi bật:
- Cho phép tạo ra các chi tiết có hình dạng phức tạp và độ chính xác cao
- Bề mặt sản phẩm nhẵn, giảm thiểu nhu cầu gia công sau đúc
- Phù hợp cho các vật liệu khó gia công
Ứng dụng: Sản xuất các chi tiết trong ngành hàng không, nha khoa, và trang sức.
II. Đúc khuôn cát (Sand casting)
Đây là phương pháp đúc truyền thống, có từ lâu đời nhưng vẫn còn rất phổ biến hiện nay. Khuôn đúc được làm từ cát và chỉ sử dụng một lần. Phương pháp này thích hợp cho việc sản xuất các chi tiết có kích thước và hình dạng đa dạng.
Đặc điểm nổi bật:
- Linh hoạt trong việc tạo ra các chi tiết có kích thước và hình dạng đa dạng
- Chi phí đầu tư thấp, phù hợp cho sản xuất số lượng nhỏ
- Có thể đúc được hầu hết các loại kim loại
Ứng dụng: Sản xuất các chi tiết máy lớn, khung máy, và các sản phẩm có yêu cầu độ chính xác trung bình.
III. Đúc khuôn kim loại (Die casting)
Phương pháp này sử dụng khuôn đúc bằng kim loại, thường là thép. Kim loại nóng chảy được đổ vào khuôn dưới áp lực cao. Phương pháp này cho phép sản xuất hàng loạt các chi tiết có độ chính xác cao và bề mặt nhẵn.
Đặc điểm nổi bật:
- Cho phép sản xuất hàng loạt với tốc độ cao
- Tạo ra sản phẩm có độ chính xác và độ nhẵn bề mặt cao
- Tiết kiệm nguyên liệu và giảm thiểu công đoạn gia công sau đúc
Ứng dụng: Sản xuất các chi tiết nhỏ, phức tạp trong ngành ô tô, điện tử, và hàng tiêu dùng.
Cần lưu ý rằng ‘Đúc khuôn kim loại’ và ‘Đúc áp lực’ thường được sử dụng thay thế cho nhau trong ngành công nghiệp. Cả hai đều chỉ quá trình đúc kim loại nóng chảy vào khuôn kim loại dưới áp lực cao.
IV. Đúc áp lực (Pressure die casting)
Đây là một biến thể của phương pháp đúc khuôn kim loại, trong đó kim loại nóng chảy được bơm vào khuôn dưới áp lực rất cao. Phương pháp này cho phép tạo ra các chi tiết phức tạp với độ chính xác cao và bề mặt hoàn thiện tốt.
Đặc điểm nổi bật:
- Tạo ra các chi tiết có độ chính xác rất cao
- Bề mặt sản phẩm hoàn thiện tốt, giảm thiểu nhu cầu gia công sau đúc
- Chu kỳ sản xuất nhanh, phù hợp cho sản xuất hàng loạt
Đúc áp lực có hai loại chính:
- Đúc áp lực buồng nóng: Phù hợp cho các kim loại có nhiệt độ nóng chảy thấp như kẽm, chì.
- Đúc áp lực buồng lạnh: Thích hợp cho các kim loại có nhiệt độ nóng chảy cao hơn như nhôm, đồng.
Ứng dụng: Sản xuất các chi tiết phức tạp trong ngành hàng không, ô tô, và thiết bị y tế.
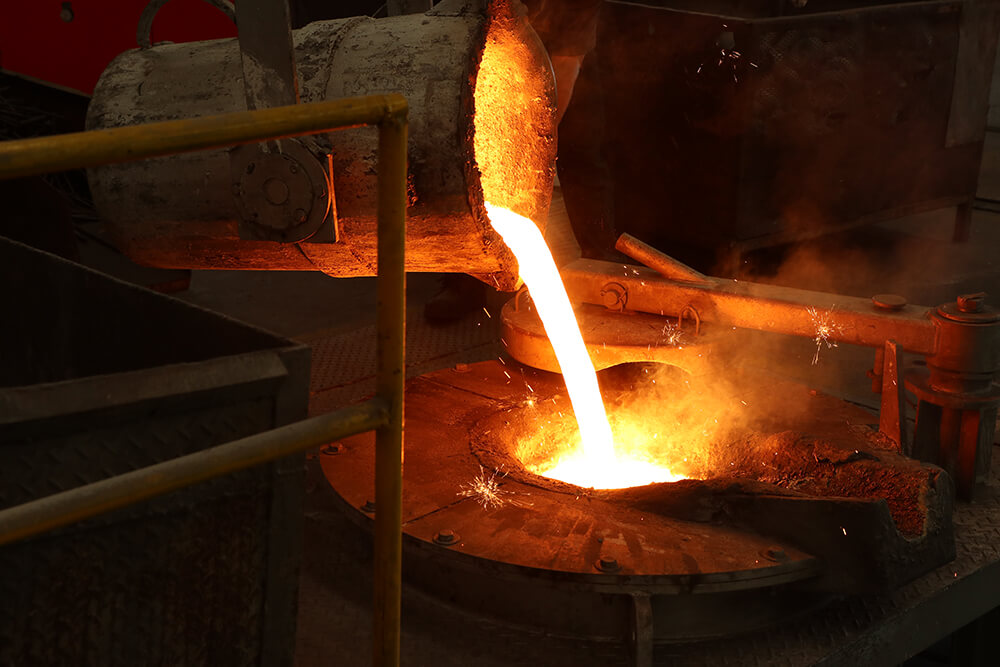
V. Đúc ly tâm (Centrifugal casting)
Trong phương pháp này, kim loại nóng chảy được đổ vào một khuôn quay với tốc độ cao. Lực ly tâm đẩy kim loại vào các góc của khuôn, tạo ra các sản phẩm có hình dạng đối xứng như ống, xy-lanh.
Đặc điểm nổi bật:
- Tạo ra các sản phẩm có cấu trúc đồng nhất
- Giảm thiểu khuyết tật do khí và tạp chất
- Phù hợp cho các sản phẩm có hình dạng đối xứng
Đúc ly tâm có ba dạng chính:
- Đúc ly tâm thật: Tạo ra các sản phẩm hình trụ rỗng.
- Đúc bán ly tâm: Sử dụng lõi để tạo ra các sản phẩm đối xứng trục.
- Đúc ly tâm ống: Tạo ra các ống ngắn hoặc vòng.
Ứng dụng: Sản xuất ống, xy-lanh, và các chi tiết hình trụ trong ngành công nghiệp nặng.
VI. Đúc kim loại áp suất thấp (Low pressure die casting)
Đây là quá trình đúc kim loại nóng chảy vào khuôn đúc bằng cách sử dụng áp suất khí thấp (thường từ 0.3 đến 1.5 bar) để đẩy kim loại nóng chảy từ dưới lên trên, vào trong khuôn. Phương pháp này thường được sử dụng cho các kim loại có nhiệt độ nóng chảy thấp như nhôm và magiê.
Đặc điểm nổi bật:
- Kiểm soát tốt quá trình đổ kim loại, giảm thiểu khuyết tật
- Tiết kiệm nguyên liệu
- Phù hợp cho các kim loại có nhiệt độ nóng chảy thấp
- Phương pháp này còn có ưu điểm là giảm khuyết tật do co ngót và tạo ra cấu trúc hạt mịn, cải thiện tính chất cơ học của sản phẩm.
Ứng dụng: Sản xuất các chi tiết bằng nhôm và magiê trong ngành ô tô và hàng không.
VII. Đúc chân không (Vacuum casting)
Trong phương pháp này, quá trình đúc diễn ra trong môi trường chân không. Điều này giúp loại bỏ các khí và tạp chất, cho phép sản xuất các chi tiết có chất lượng cao và ít khuyết tật.
Đặc điểm nổi bật:
- Tạo ra sản phẩm có chất lượng cao và ít khuyết tật
- Phù hợp cho các vật liệu dễ bị oxy hóa
- Kiểm soát tốt cấu trúc vi mô của sản phẩm
- Phương pháp này đặc biệt hiệu quả trong việc tạo ra các chi tiết có thành mỏng và hình dạng phức tạp mà các phương pháp đúc khác khó thực hiện được.
Ứng dụng: Sản xuất các chi tiết chính xác cao trong ngành hàng không, vũ trụ, và y tế.
Như vậy, chúng ta đã tìm hiểu về 7 phương pháp đúc kim loại phổ biến nhất hiện nay cùng những đặc điểm nổi bật của từng phương pháp. Mỗi phương pháp đều có những ưu nhược điểm riêng và phù hợp với các ứng dụng cụ thể khác nhau.
Việc lựa chọn phương pháp đúc phù hợp phụ thuộc vào nhiều yếu tố như loại kim loại, hình dạng và kích thước chi tiết, yêu cầu về độ chính xác, số lượng sản xuất và chi phí. Hiểu rõ về các phương pháp đúc sẽ giúp các kỹ sư và nhà sản xuất đưa ra quyết định tốt nhất cho từng ứng dụng cụ thể, góp phần nâng cao hiệu quả sản xuất và chất lượng sản phẩm.